RMR® -
Riserless Mud Recovery
DRILL YOUR TOP-HOLES WITH ENGINEERED MUD AND FULL RETURNS TO THE RIG. SAVE TIME, MONEY AND THE ENVIRONMENT
What is RMR®
The RMR® Riserless Mud Recovery system is a risk-reduction tool that enables the drilling of a better quality, more stable top-holes - safer, quicker and with less environmental impact. This Dual Gradient Drilling system is an innovative way to return mud and cuttings to the rig before the marine riser is run, without discharge to the seabed. With RMR® there is no 'Pump & Dump'.
Thanks to its closed-loop design, engineered fluids can be used on the top-hole section and recycled - which makes sense safety-wise, environmentally and financially.
Where Do You Apply RMR® Technology
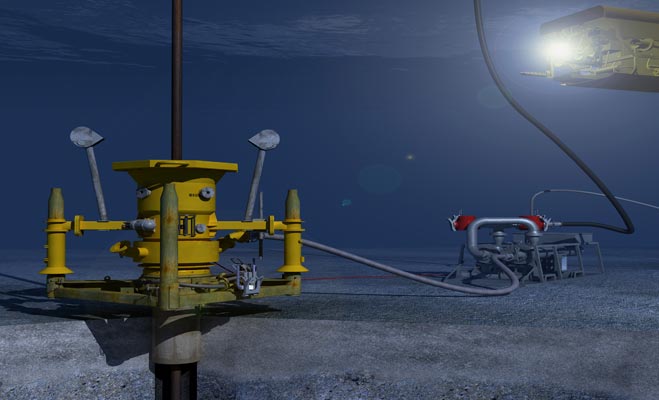
Top-hole instability
Top-hole instability can threaten the integrity of the entire well structure. The top-hole section is the structure that the rest of the well relies on.
Environmentally Sensitive Areas
How RMR® Can Help You
- Primary well control before BOP/riser installed
- Ability to check for shallow-hazard influx without a pilot hole
- Improved hole stability
- Deeper surface casing
- Fewer casing strings
- Top-hole mud-log data and cuttings
- No cement top-up jobs required
- Zero discharge at seabed
Safety Advantages
- Safe identification of gas
- Better conductor/Xmas Tree stability
- Mud volume control in surface hole
- Fast gain/loss indication
- Real-time visual monitoring of the well
- No smothering of seabed by cuttings
- Lower risk of undermining well/template
Experience
Using the system, an operator eliminated a 20" casing and successfully set 13 5/8" surface casing down to more than 2,350m (7,710ft). The system has been deployed from shallow waters down to more than 1,400 m (4,600 ft) in deep water application.
.png?width=2000&height=588&name=Untitled%20design(22).png)
How RMR® Works
The RMR® system has an electrical pump (SPM) placed on the seabed, and a funnel (SMO) on top of the Subsea Wellhead. By connecting a suction hose between the funnel and the subsea pump, the system pumps out mud, cuttings and debris coming from the well, and returns it to surface and over the shakers through the return line. The level of mud in the funnel is constantly monitored by cameras and pressure sensors to make sure that everything is pumped to surface and nothing is spilled to sea. The suction point is placed as low as possible on the funnel to also make sure that seawater does not contaminate the mud that is pumped back to surface.
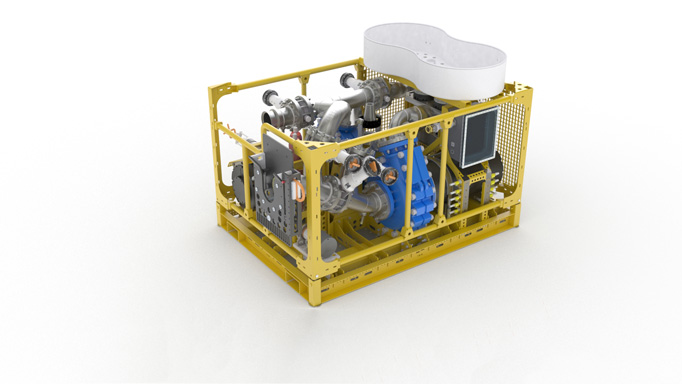
Case Studies
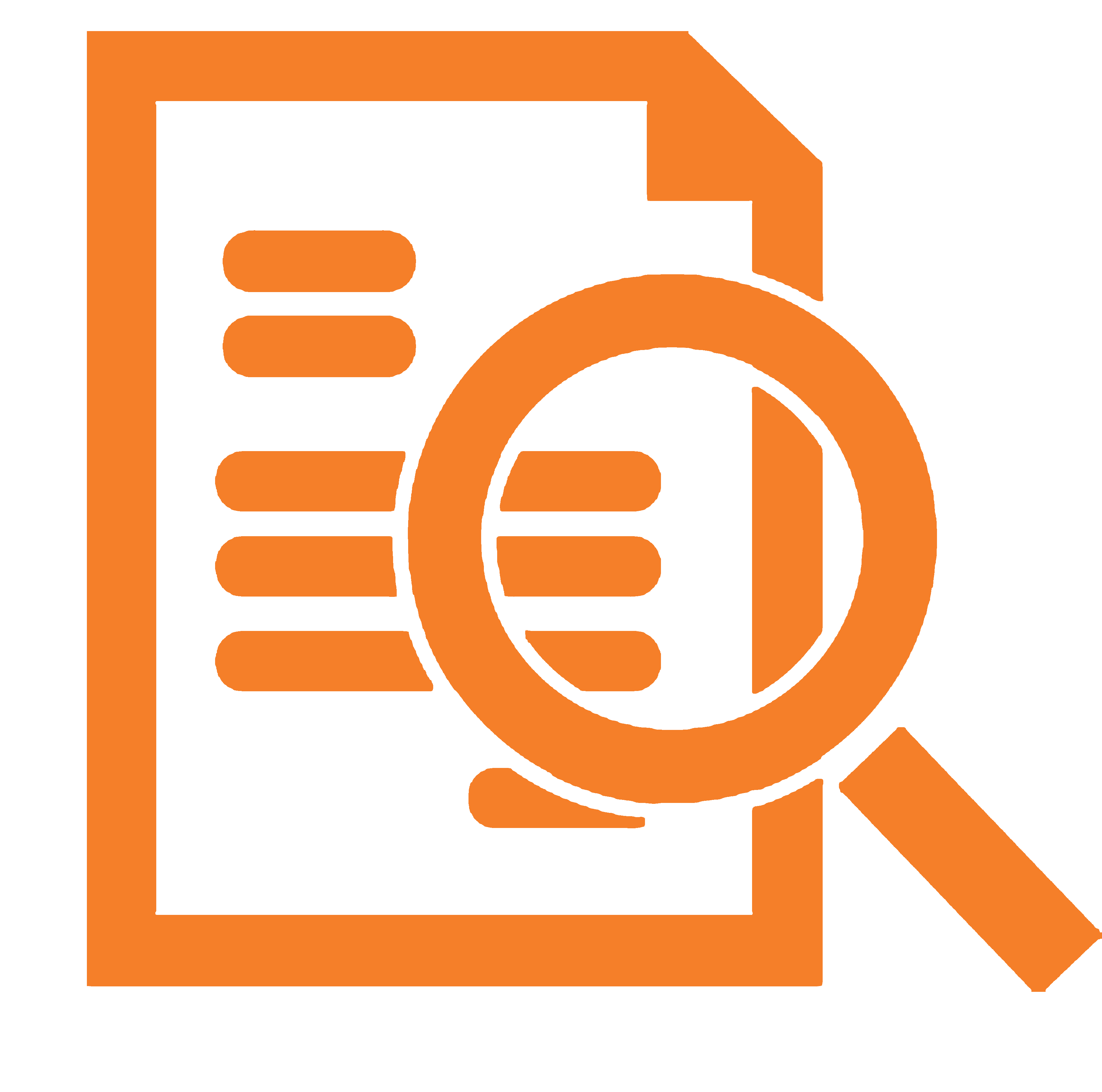
1. BP, Caspian Sea
Problems with shallow formations forced BP to abandon its West Azeri template in the Caspian Sea. Read how they solved their issue using RMR® technology
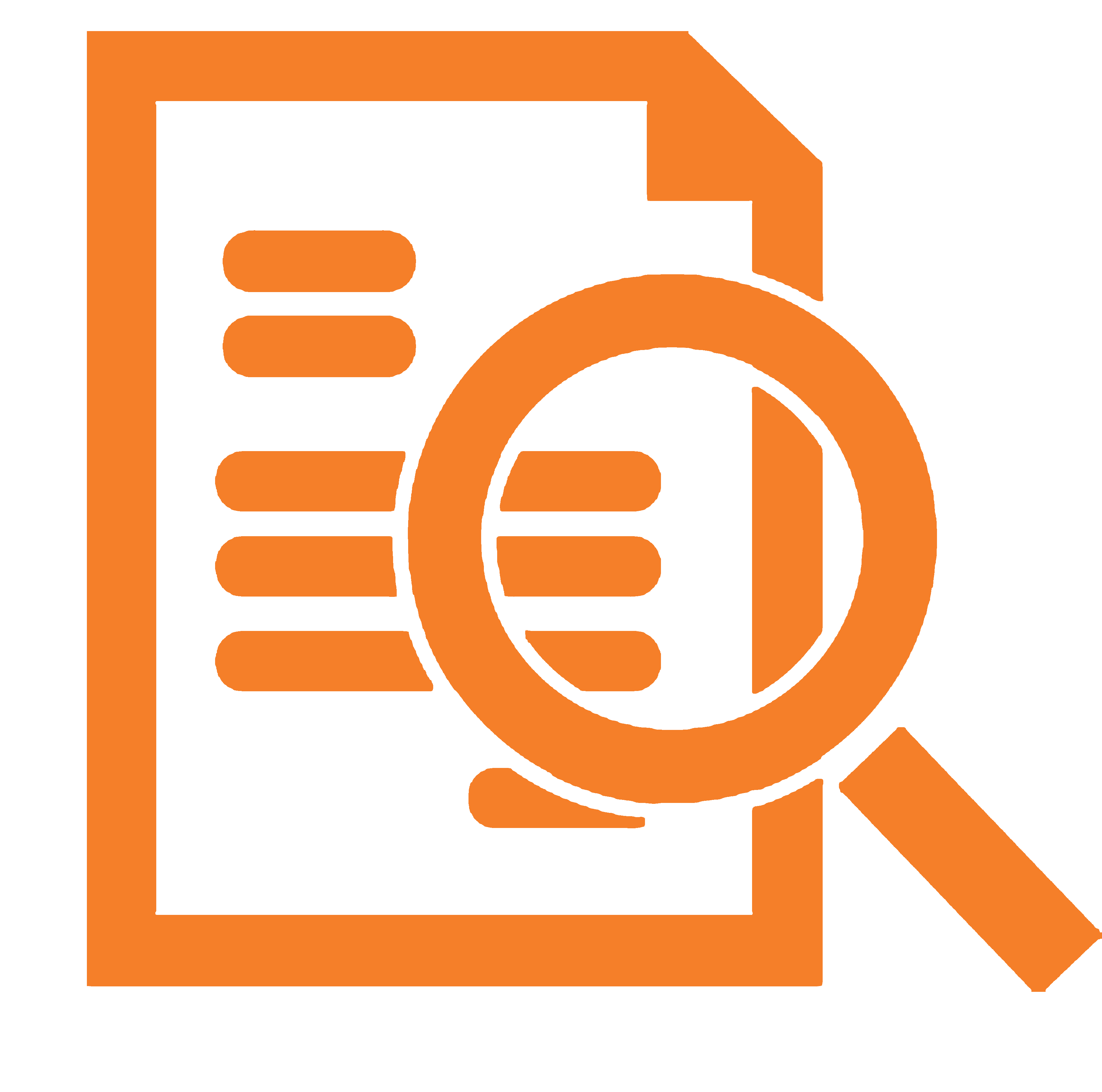
2. CNR, UK North Sea
Hole instability problems with stuck pipe led to well abandonments. Read how RMR® was used to solve this issue, which resulted in a stable hole with no problems and the fastest 20” casing run.
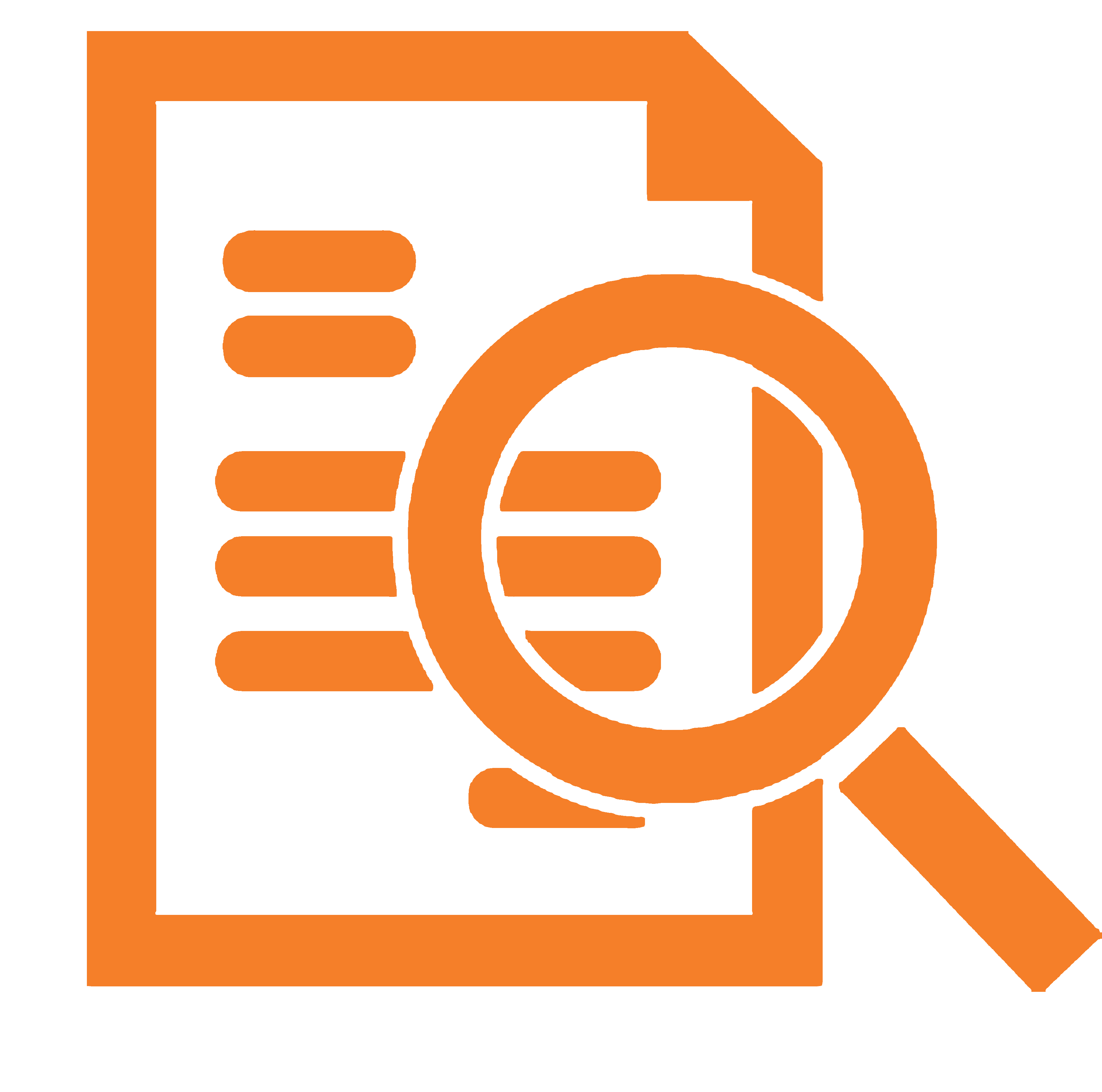
3. BP, Sakhalin Island
Russian environmental protection regulations forbid any discharge of cuttings after the conductor is set. Read about how these reguations were met using the RMR® system.
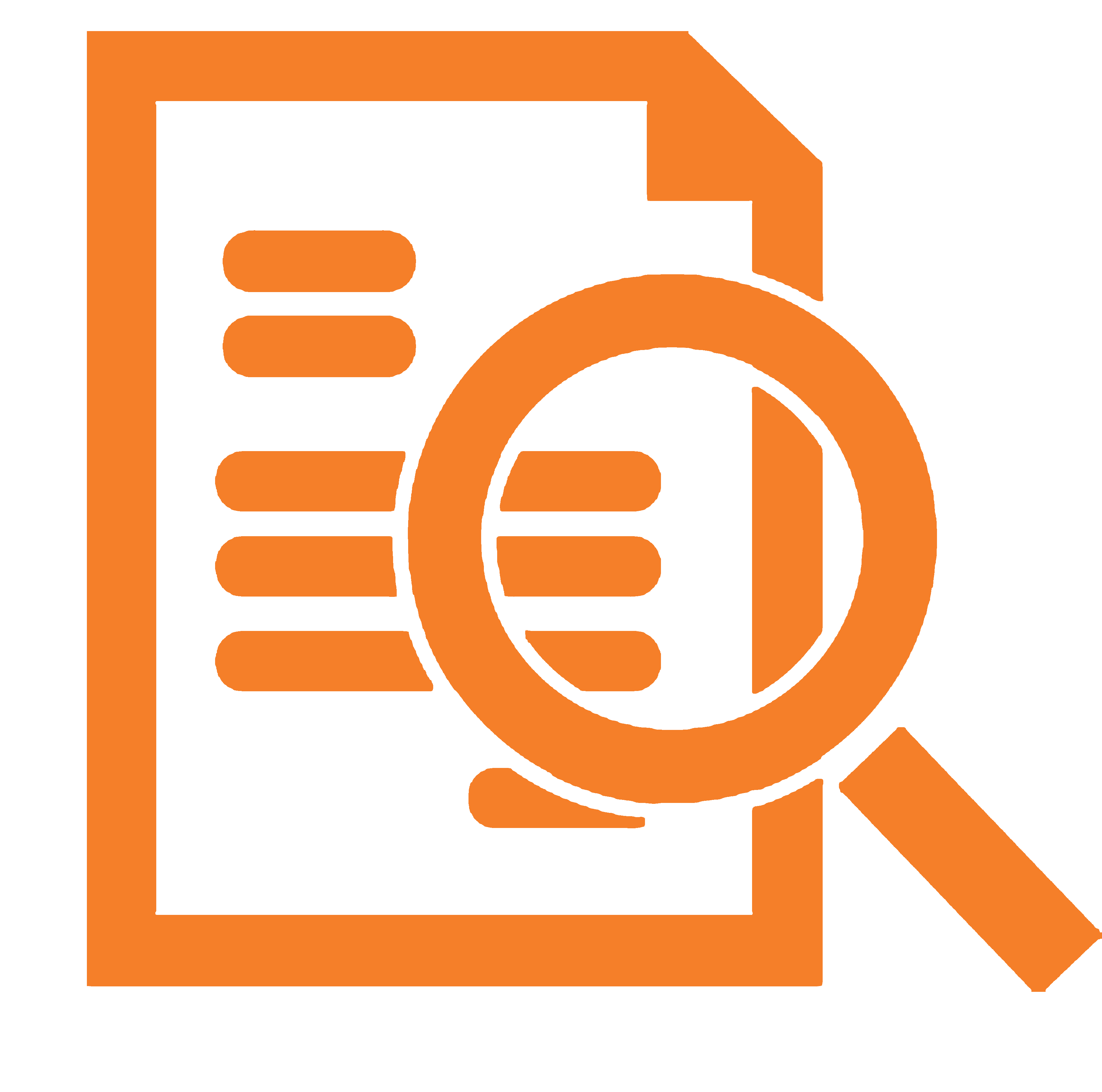
4. BP, Egypt
BP Egypt wished to install service casing at about 1,085m. However, experienced a lot challenges. Read about how standard RMR® equipment was modified for this operation.
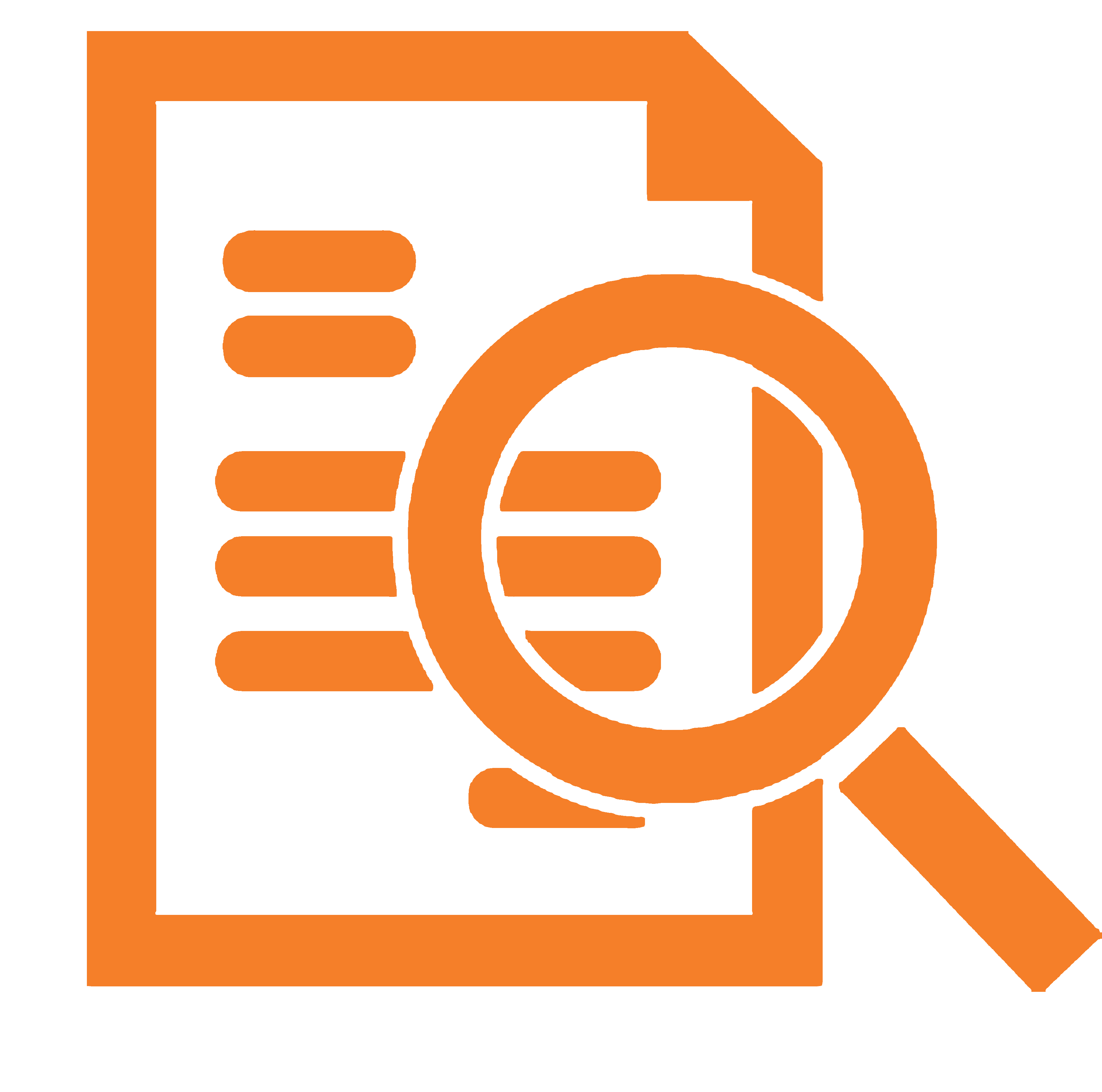
5. INPEX, Browse Basin
Soft sand tends to fall into the wellbore, causing pack-offs and stuck pipe, which can prevent casing being run to dept. Read how this issue was solved using RMR® without the extra time and cost of 20”casing.
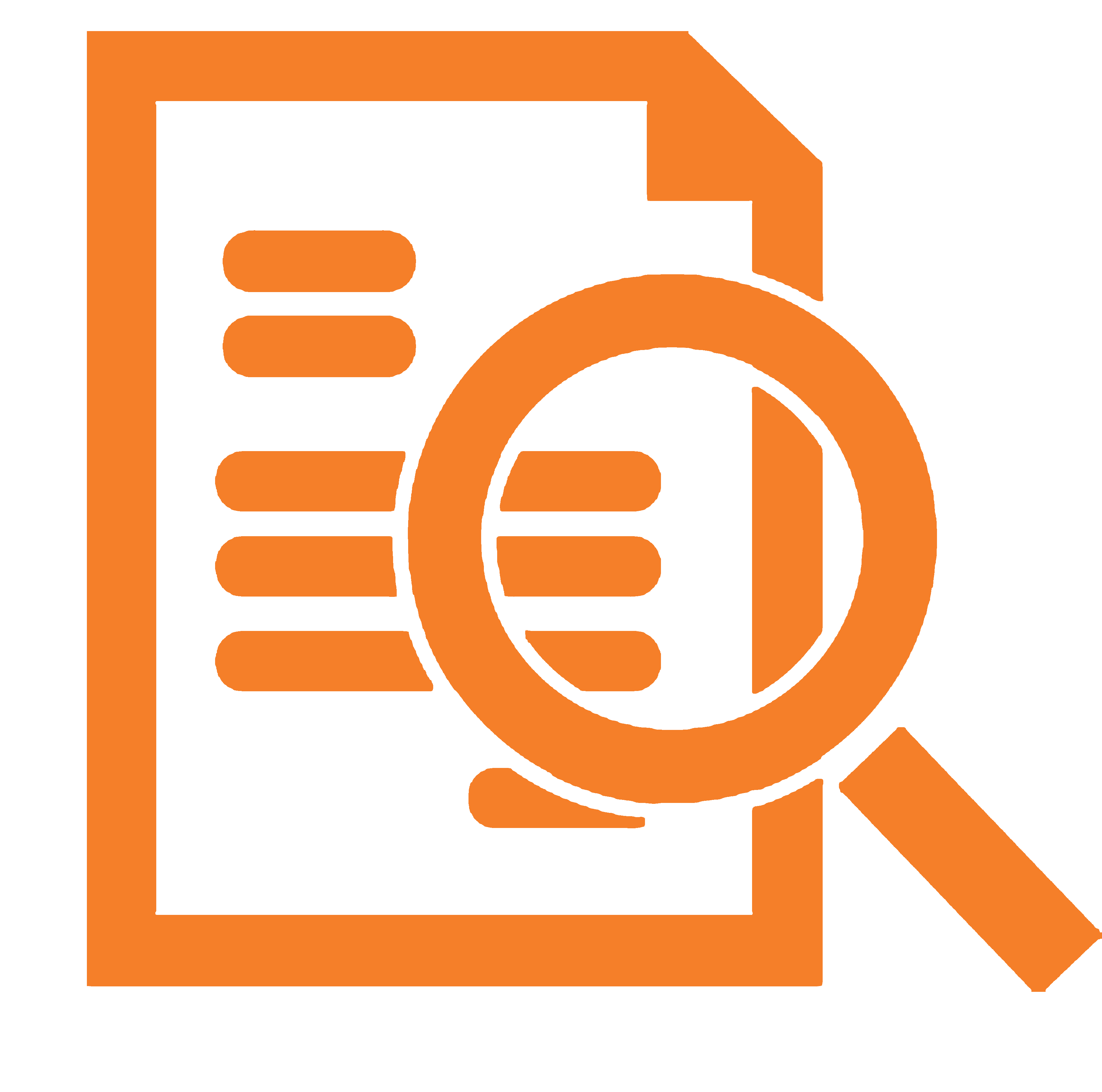
6. Equinor, Gulf of Mexico
Statoil planned to drill an exploration well in an area known for shallow geo-hazards. Read how RMR® was used in order to minimise risks.
Watch the RMR® technology animation
Brochure
strings.
Get in depth knowledge about the RMR® system by reading our product material.