Case Studies
Case Studies With EC-Drill® Technology
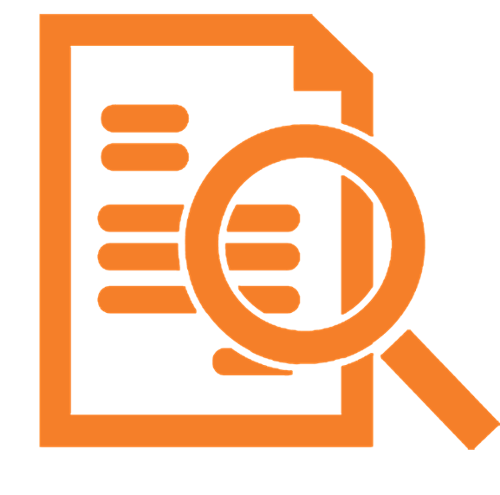
EC-Drill® Dual MPD Influx Management
EC-Drill®Dual MPD system safely circulating out influx with zero operating margin in Deepwater well. Safely circulating out an influx in a Deepwater well with zero operating margin. In addition to narrow operating windows the friction from the long Chokeline makes it difficult to circulate out the influx, while other well control methods are time consuming.
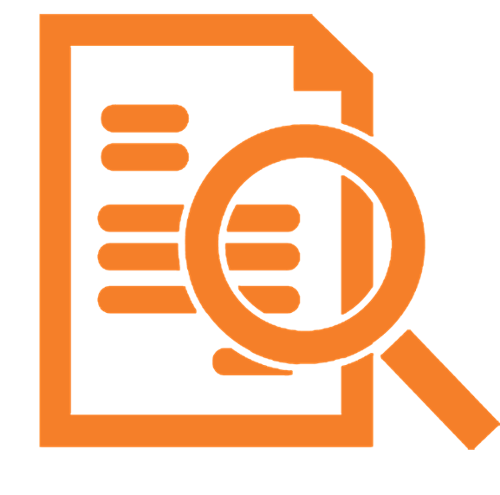
EC-Drill® Dual Gradient in Deepwater Drilling
Learn how the Operator wanted to reduce the number of casing strings while maintaining ahigh average ROP through the section, and EC-Drill® reduced casing points in Deepwater Drilling. A common challenge for Deepwater wells is the need for multiple sections.
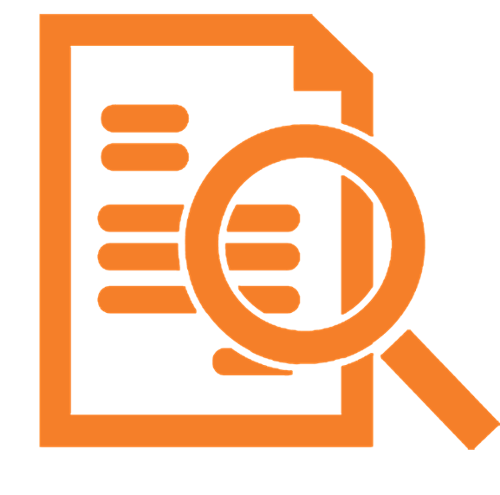
EC-Drill® RMR® - Providing Large Savings for Shell
Learn how Shell had to have RMR® and EC-Drill®, to drill a undrillable well in the Ormen Lange campaign in Norway. EC-Drill® was identified as the best technology to handle the gravel packing, drilling, casing, and cementing in the narrow pore pressure.
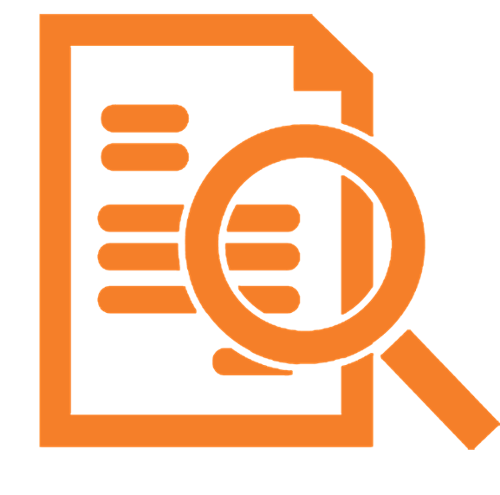
EC-Drill® RMR® - Drilling the undrillable for Shell
Learn how a multi-national operator recently used EC-Drill®’s instant kick detection service to complement and enhance conventional kick detection methods during deep-water exploratory drilling in the Gulf of Mexico.
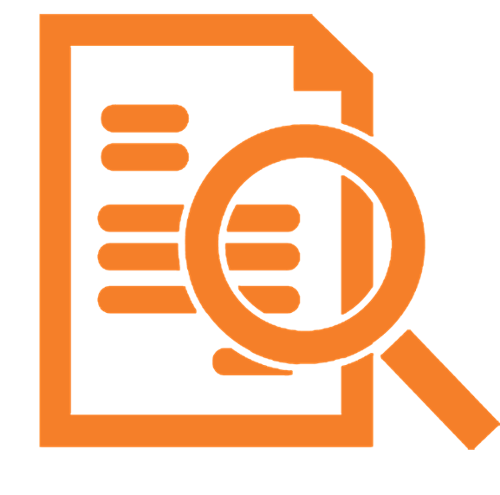
EC-Drill® - Instant kick detection in GoM
Learn how a multi-national operator recently used EC-Drill®’s instant kick detection service to complement and enhance conventional kick detection methods during deep-water exploratory drilling in the Gulf of Mexico.
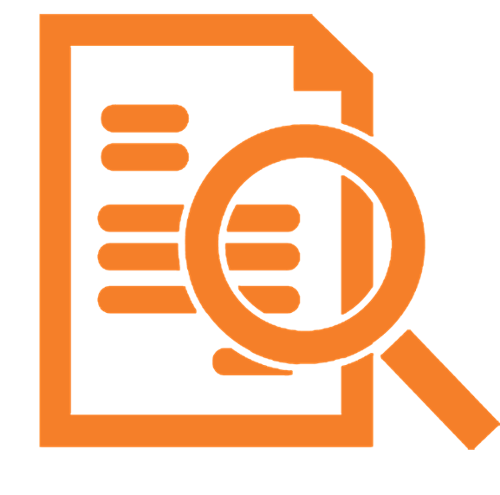
EC-Drill® benefits displayed on Shah Deniz
Learn how BP drilled a top-hole section on the Caspian’s Shah Deniz field through hazardous formations in terms of shallow water/gas flow from a fixed platform using EC-Drill® technology
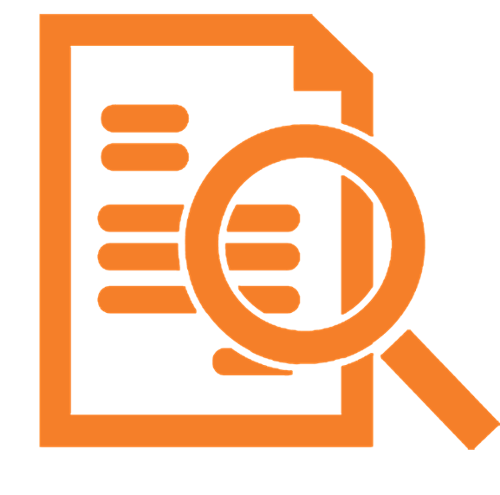
EC-Drill® saves rig time on the Troll field
Learn how the EC-Drill® technology was able to eliminate tripping speed constraint for running screen on the Troll field, increasing tripping speed by 50 per cent
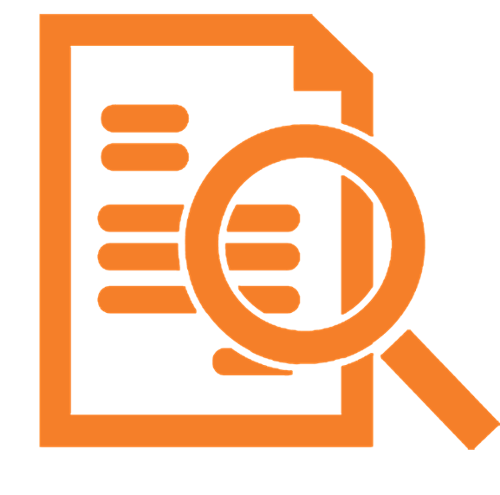
EC-Drill® extends well length
Find out how EC-Drill® technology helped reduce mud losses and saved operator the associated costs on the depleted Troll field in the North Sea.
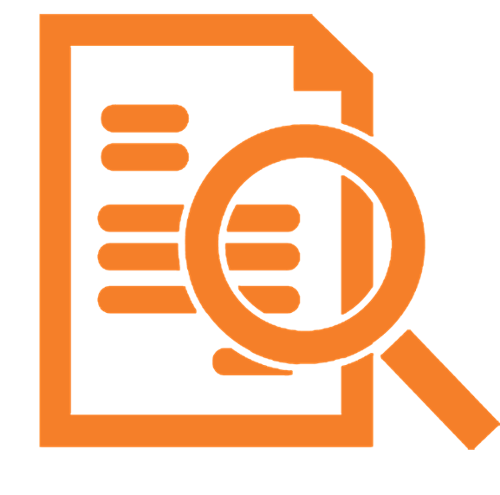
EC-Drill® World first Managed Pressure OHGP
Find out how EC-Drill® technology enabled a major operator to perform an industry first Managed Pressure Open Hole Gravel Pack (OHGP) to achieve Best-in-class wells.
Case Studies With RMR® Technology
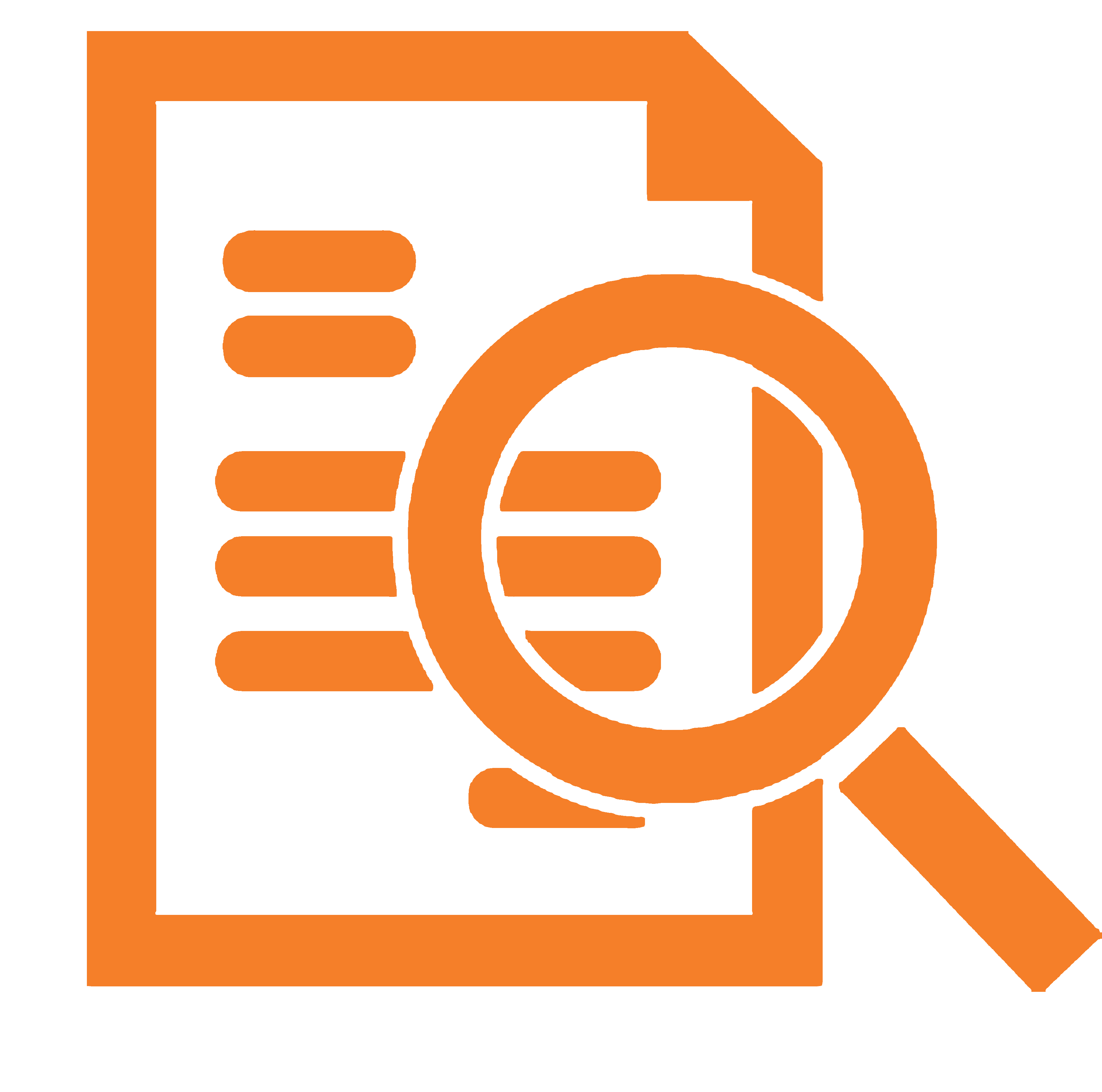
1. BP, Caspian Sea
Problems with shallow formations forced BP to abandon its West Azeri template in the Caspian Sea. Read how they solved their issue using RMR® technology
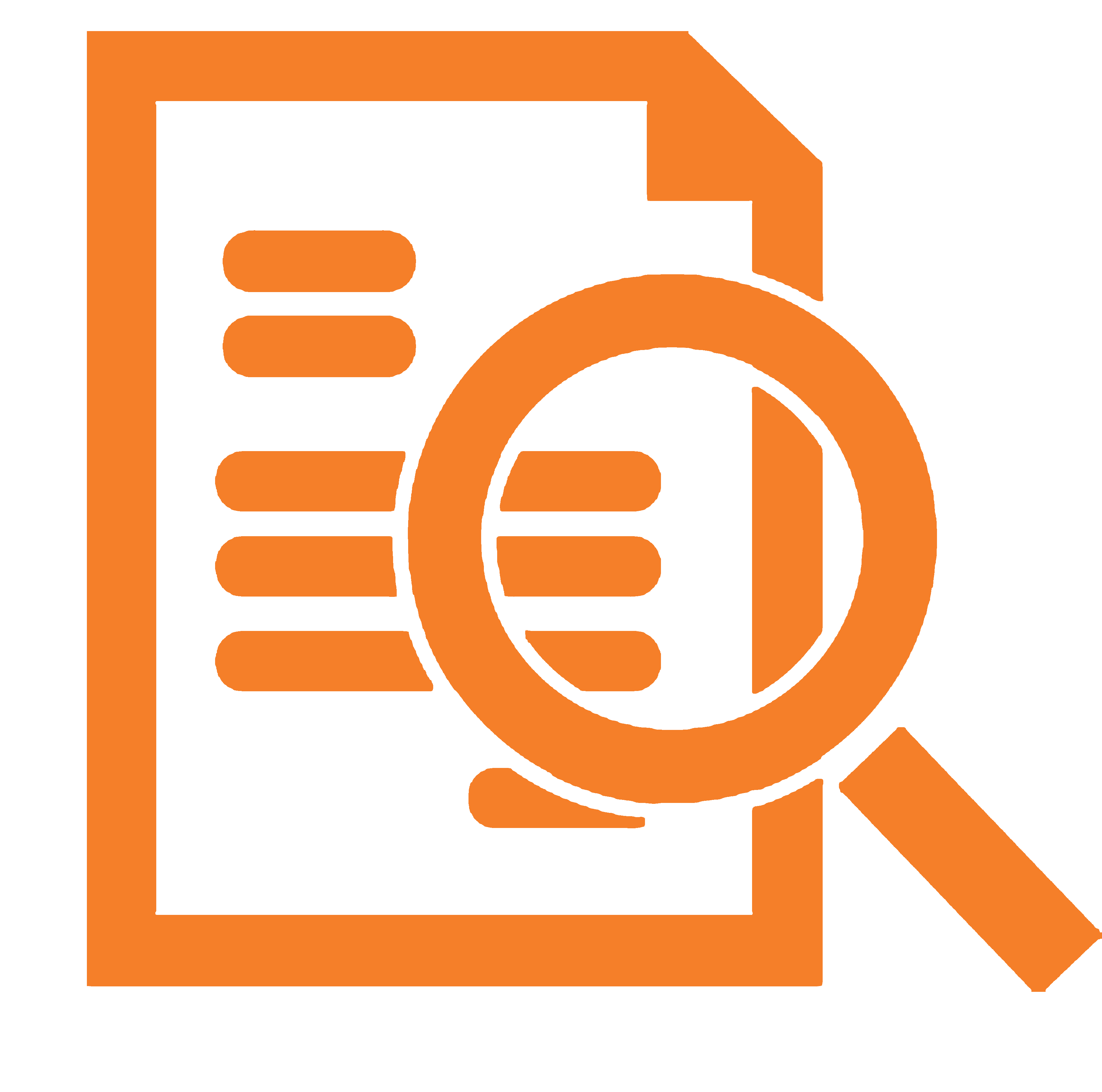
2. CNR, UK North Sea
Hole instability problems with stuck pipe led to well abandonments. Read how RMR® was used to solve this issue, which resulted in a stable hole with no problems and the fastest 20” casing run.
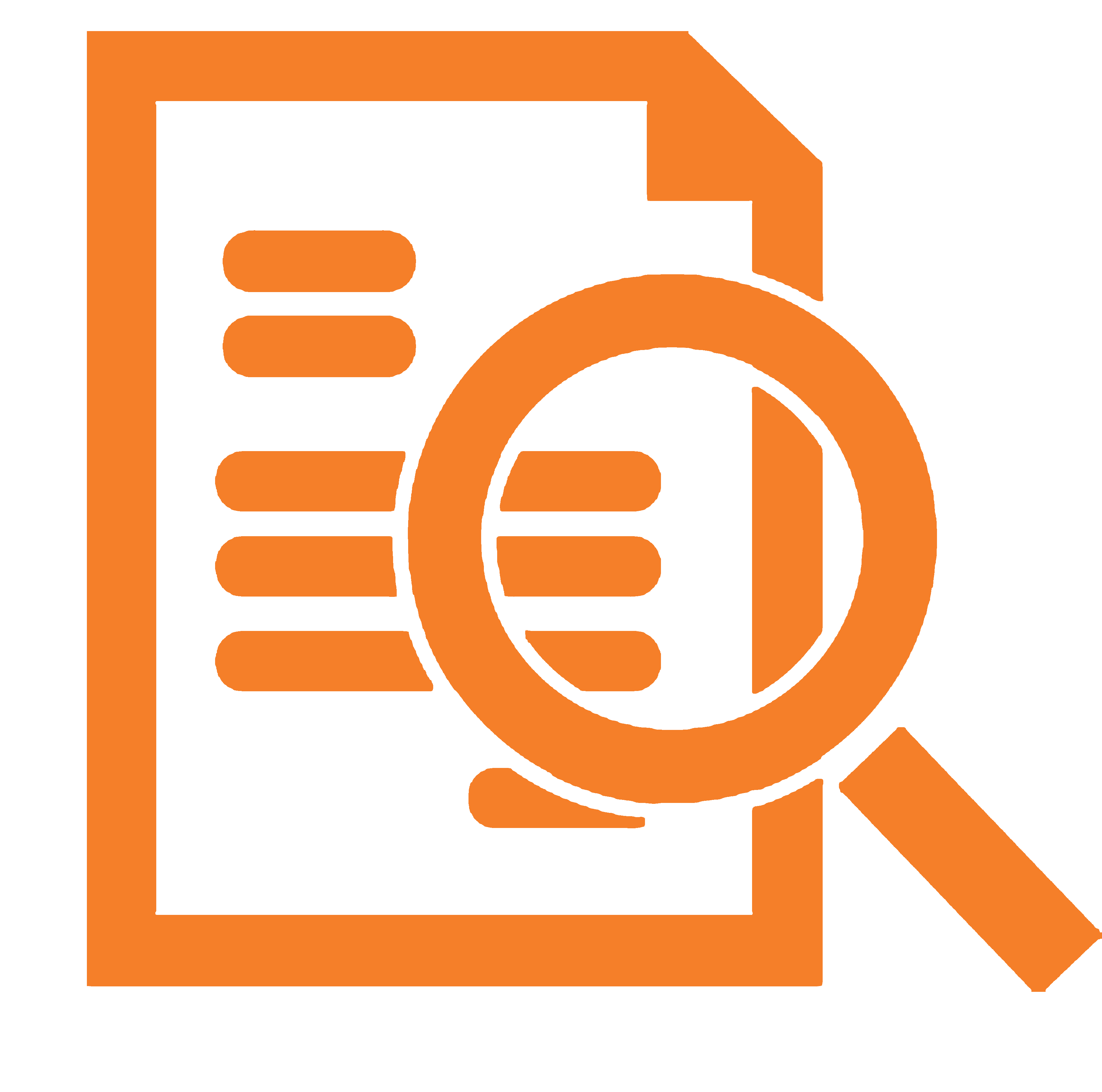
3. BP, Sakhalin Island
Russian environmental protection regulations forbid any discharge of cuttings after the conductor is set. Read about how these reguations were met using the RMR® system.
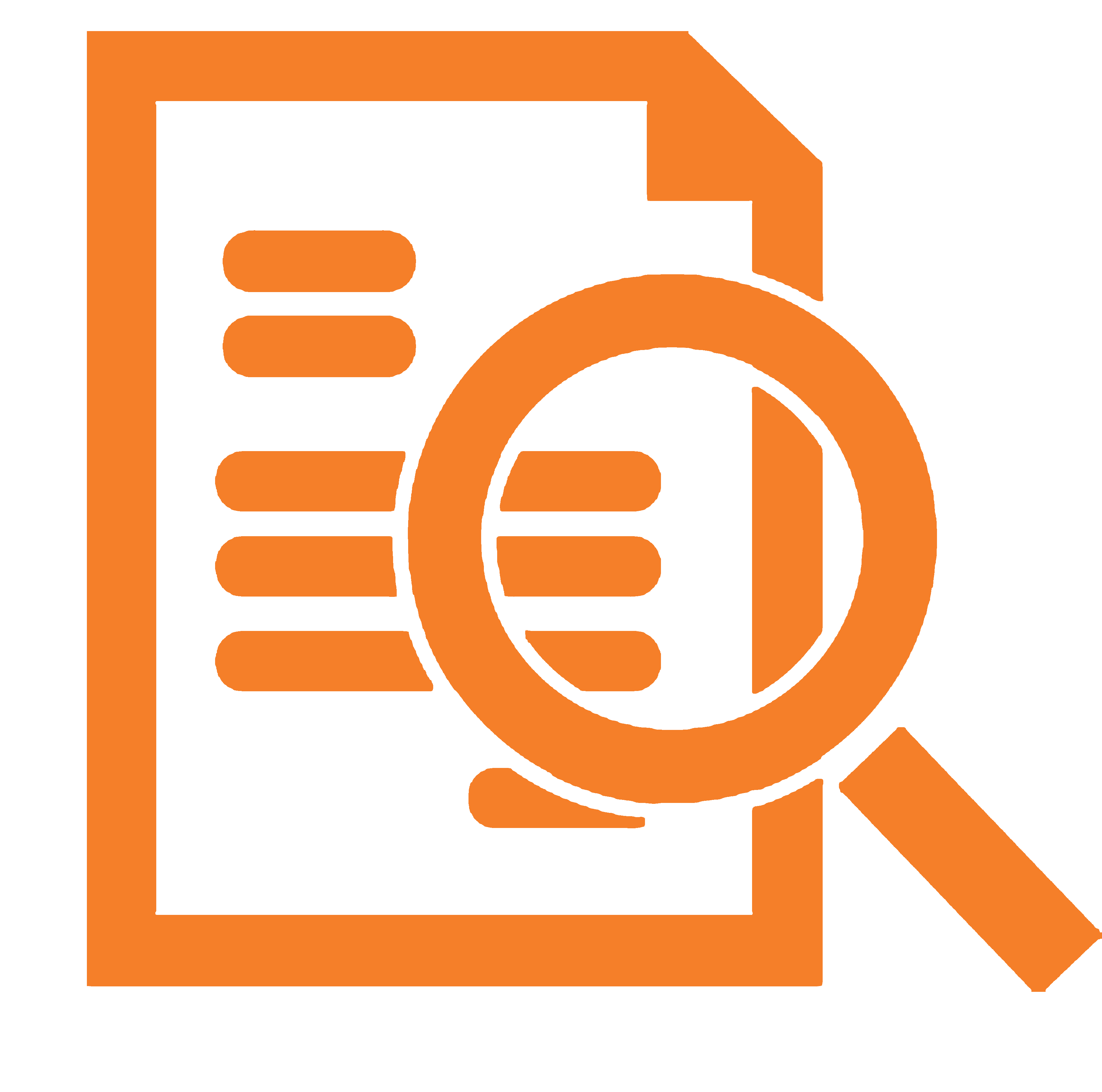
4. BP, Egypt
BP Egypt wished to install service casing at about 1,085m. However, experienced a lot challenges. Read about how standard RMR® equipment was modified for this operation.
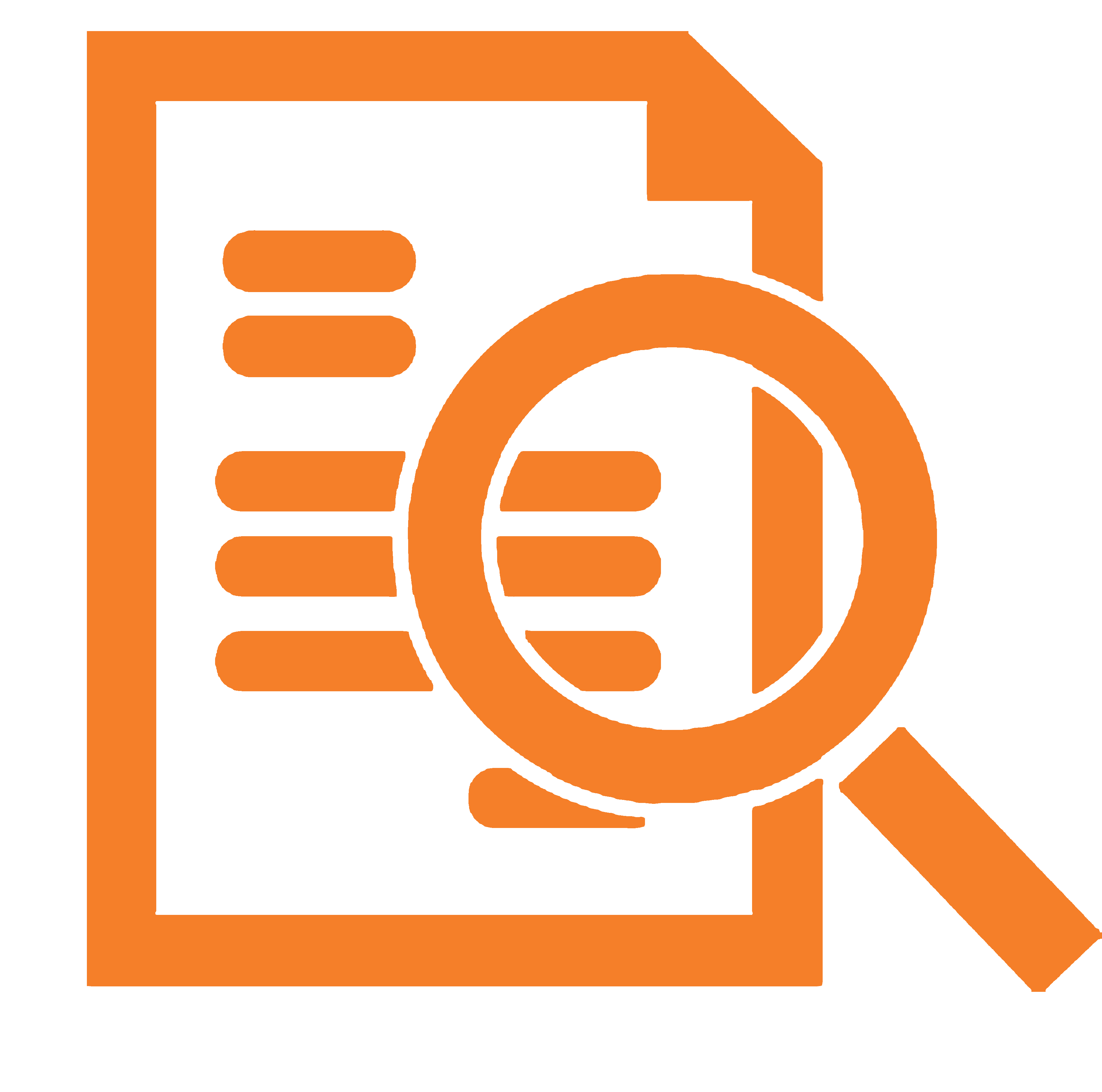
5. INPEX, Browse Basin
Soft sand tends to fall into the wellbore, causing pack-offs and stuck pipe, which can prevent casing being run to dept. Read how this issue was solved using RMR® without the extra time and cost of 20”casing.
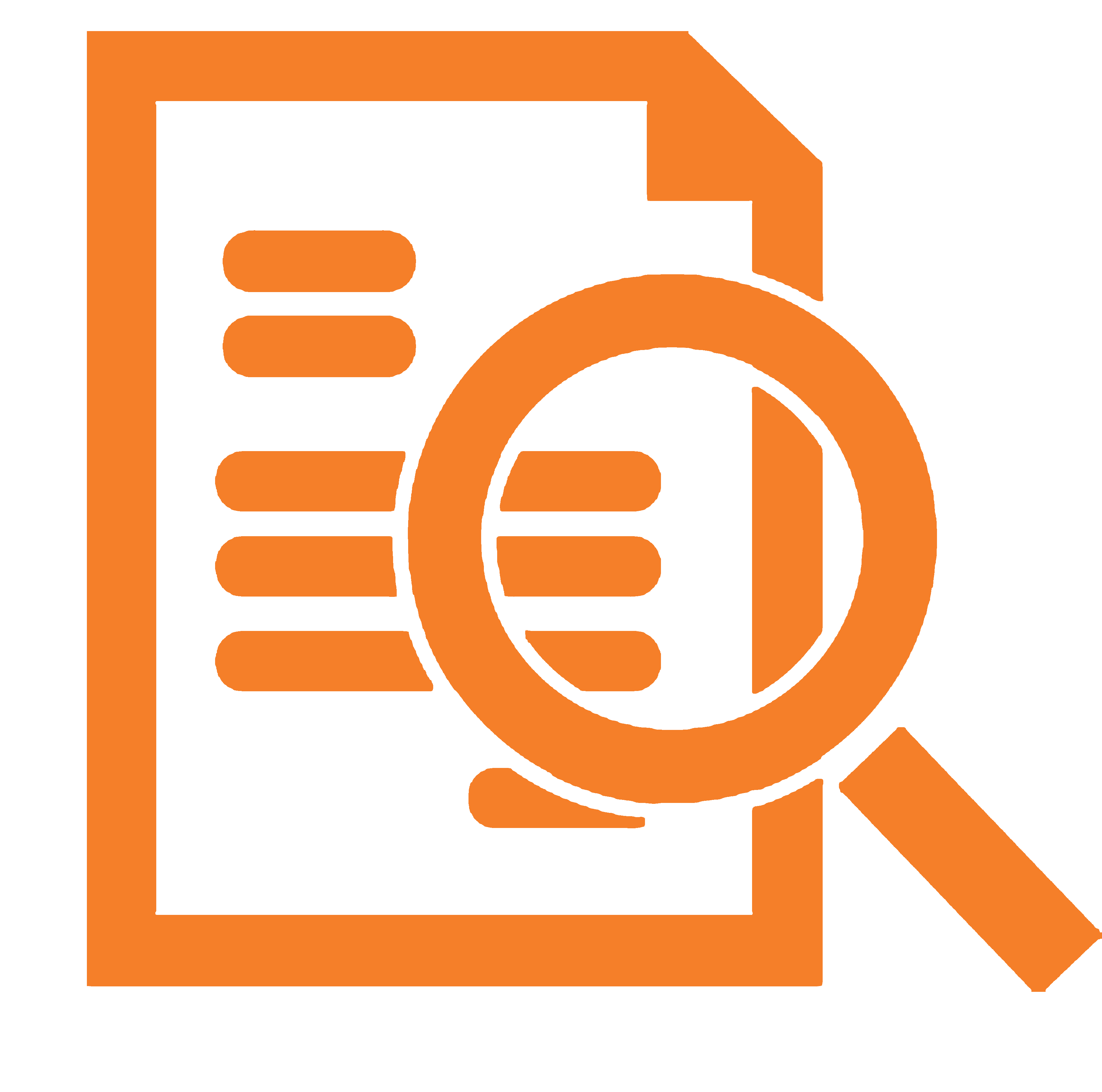
6. Equinor, Gulf of Mexico
Statoil planned to drill an exploration well in an area known for shallow geo-hazards. Read how RMR® was used in order to minimise risks.
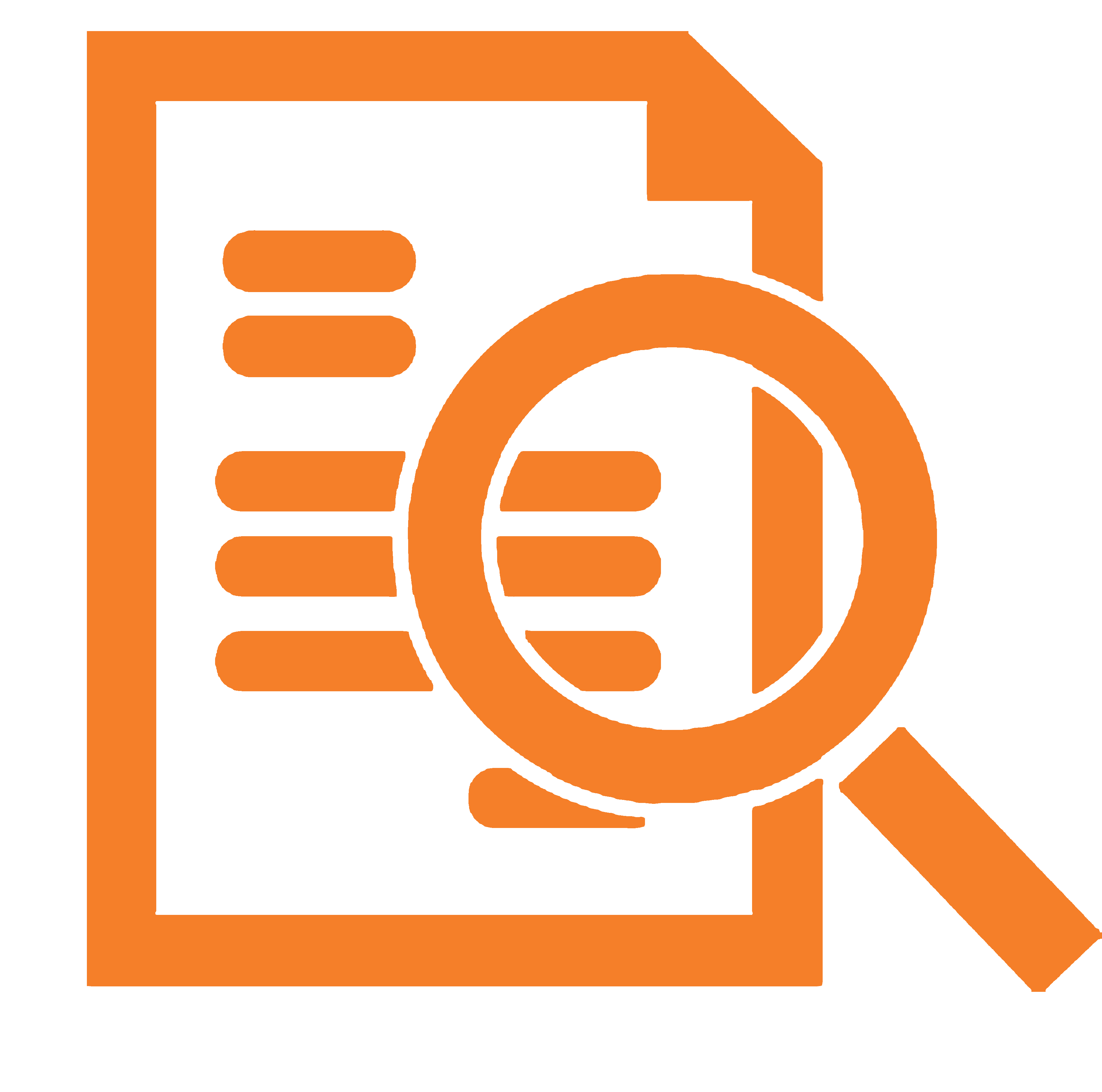
7. Ormen Lange, North Sea
A major operator in the North Sea planning to drill a subsea well was facing issues in the design of the well casing program.
Case Studies With Managed Pressure Cementing Technology
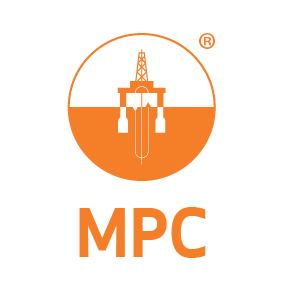
1. BP, Caspian Sea: Cement 22" Surface Casing and isolate notorious sands
The cementing of top-hole sections in narrow pressure windows has traditionally been highly problematic. This is due to cement slurry loss, shallow water and gas flow. Read about how MPC® was used to solve this problem.
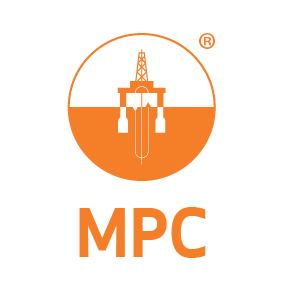
2. BP, Caspian Sea: Top-hole Cementing
Presence of high-pressure shallow water and gas in the Caspian region, notorious for its unconsolidated formations, had previously imposed a lot of costs on BP. Learn how MPC® was vital to enable effective top-hole cementing.