MPC® -
Managed Pressure Cementing
Control your pressure during and after your cement job using a conventional cement slurry.
What is MPC® Managed Pressure Cementing system
The MPC® Managed Pressure Cementing system provides safe isolation of problematic zones - cost effectively - even in challenging narrow pressure window scenarios. The system provides precise control of the pressure and flow during and after the cement job. Constant pressure can be achieved at weak zones, preventing losses to the formation. Gas and shallow water hazards are simply yet effectively kept at bay.
MPC® is a safety-enhancing system. In the case of a loss or influx, rapid action can be taken to prevent a situation from escalating. Any gain or loss can be rectified both quickly and easily.
The system, which is the perfect partner to RMR®, can use conventional cement rather than costly foam or nitrified variants yet still achieve effective isolation.
Where Do you Apply MPC® Technology?
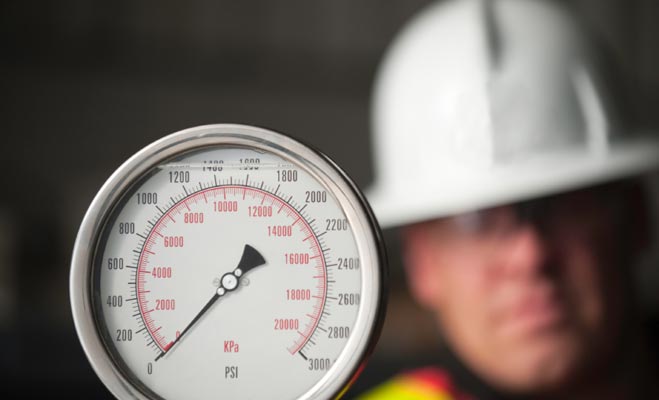
Problematic Zones
Problematic zones are the source of well-threatening challenges such as influx and losses, especially in narrow pressure window scenarios.
Managed Pressure Cementing
Shallow Flow Hazards
Drilling Top-Holes
What MPC® Technology Can Do For You
- Give the ability to verify cement at surface
- It enables the monitoring of pressure during set-up.
- Pressure can be applied to verify that the barrier is in place.
- Improved pressure manipulation enables effective drilling of depleted reservoirs and narrow pressure windows
- Enhanced safety thanks to the system’s rapid kick/ loss detection
- Significant cost and time savings thanks to efficient mitigation of pressure-regime related issues
- The ability to set deeper surface casing
- Superior wellbore integrity
- Reduced logistics requirements
How MPC® Technology Works
With traditional cementing techniques, the challenge has always been to effectively isolate shallow gases and water in the top-hole section where unstable, unconsolidated formations exist.
Low fracture gradients combined with high-density slurries and circulation pressure mean that the chances of fracturing the formation are high, resulting in losses.
The MPC® system allows the operator to unload the pressure as the heavier fluid (spacer, cement slurry) flows up the annulus above the critical zone in order to compensate for higher hydrostatic pressure. MPC® keeps the wellbore pressure at the critical zone constant.
The result? No losses and a cement job you can depend on.
With conventional cementing technique in the setting stage, a loss in hydrostatic pressure brings with it an increase in the likelihood of a fluid-bearing formation flowing into the annulus- which could ultimately lead to well-abandonment.
Case Studies
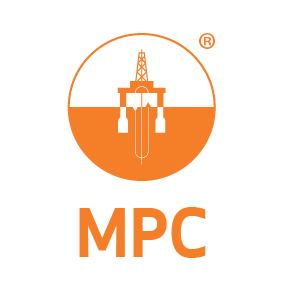
1. BP, Caspian Sea: Cement 22" Surface Casing and isolate notorious sands
The cementing of top-hole sections in narrow pressure windows has traditionally been highly problematic. This is due to cement slurry loss, shallow water and gas flow. Read about how MPC® was used to solve this problem.
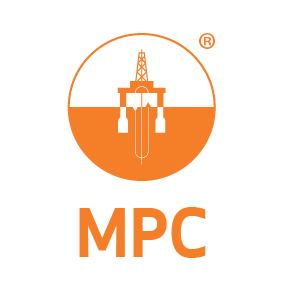
2. BP, Caspian Sea: Top-hole Cementing
Presence of high-pressure shallow waterand gas in the Caspian region, notoriousfor its unconsolidated formations, hadpreviously imposed a lot of costs on BP. Learn how MPC® was vital to enable effective top-hole cementing.
Watch how the MPC®-Managed Pressure Cementing system works.