Shallow Flow Hazards
Shallow Flow Hazards
Formations part of the top-hole sections can contain water and gas that has the potential to flow to seabed if not properly controlled. They are labeled as shallow because they are located in the top-hole sections. Shallow water and gas flow hazards are common in many offshore, especially Deepwater, wells.
Why is This a Challenge
Shallow flow hazards are typically encountered before the marine riser is in place. As a result, if the formation begins to flow in an uncontrolled manner then it creates a safety risk to the rig as well as the risk of damaging the structure of the well and impacting the surrounding seafloor. Shallow water floor is especially worrisome as it can lead to buckling of the casing strings and large deposits of sand on the seafloor. There is also an environmental impact if an uncontrolled release of water or gas to sea occurs.
Shallow flow can occur during any point during drilling and cementing. If flow begins during the cementing operation it can create channels in the cement column and prevent isolation, meaning the shallow formations can continue to flow after the cement operation and be extremely difficult to remediate to achieve isolation. Preventing channels forming during setting of cement adds additional challenges to the cement design.
Detecting shallow flow can be difficult as changes in the return rate at seafloor are hard to monitored with the ROV. Usually the return of drilling fluid and cuttings will make the well location cloudy and add to the difficulty of seeing the returns, or a change in returns, from the wellbore.
Seismic information and mapping of structures are used to locate shallow flow hazards, in addition to offset well information. However, it is difficult with certainty to avoid shallow flow hazards as the risk can be reduced but rarely eliminated. This add difficulty in trying to avoid the challenge of shallow flow hazards. When drilling through formations that contain shallow flow hazards or in locations that are known to contain these formations, the operator must be prepared to handle shallow flow and take the proper precautions.
What Are Your Options?
- Choose a well location that avoids the shallow flow hazard. It may not be possible to completely avoid the hazard and to some degree the hazard may always be present.
- Drill conventionally with a weighted drilling fluid. A weighted drilling fluid will provide a higher overbalance then seawater to any shallow flow zones. The weighted drilling fluid can be used as the initial drilling fluid, or as a contingency if a shallow flow hazard is encountered. As there is not marine riser, all drilling fluid is pumped to sea and there is no volume control, it can be difficult to monitor for gains or losses. This option provides little benefit to the cementing operation.
- Use Riserless Mud Recovery (RMR®) to drill entire section with a weighted drilling fluid in a closed loop system. The closed loop enables volume control during the entire drilling and cementing operations. It can accurately monitor the well for gains and losses while allowing you to respond if needed. The Managed Pressure Cementing (MPC®) supplementary system can be used to adjust the pressure during cementing operations and prevent flow from occurring during setting of cement.
How To Deal With Shallow Flow Hazards
RMR® creates a closed loop system that returns all the drilling fluid to the rig while enabling volume control during the entire drilling and cementing operations. Resulting in the ability to monitor the well and detect any gains or losses. Not only can a weighted drilling fluid be used to mitigate shallow flow hazards, but the closed loop enables monitoring of the well and primary barrier during the entire drilling operation.
MPC® enables monitoring and adjusting annulus pressure during and after cement operations. It can be used to reduce the annulus pressure while placing cement, thus reducing the risk of losses and reliance on lightweight cement slurries, and increase the annulus pressure while cement is setting up to compensate the loss of hydrostatic pressure. RMR® together with MPC® enables volume control and physical confirmation of cement to surface, offering the ability to determine top of cement and success of the cement operation
RMR®
In areas with challenging top-hole conditions, such as unconsolidated sands, it makes sense to commence drilling the top-hole with engineered, weighted fluid as you would for the down-hole sections of a well.
However, there are environmental issues to consider. The RMR® (Riserless Mud Recovery) system enables the use of engineered fluid even in environmentally sensitive areas thanks to its closed-loop design.
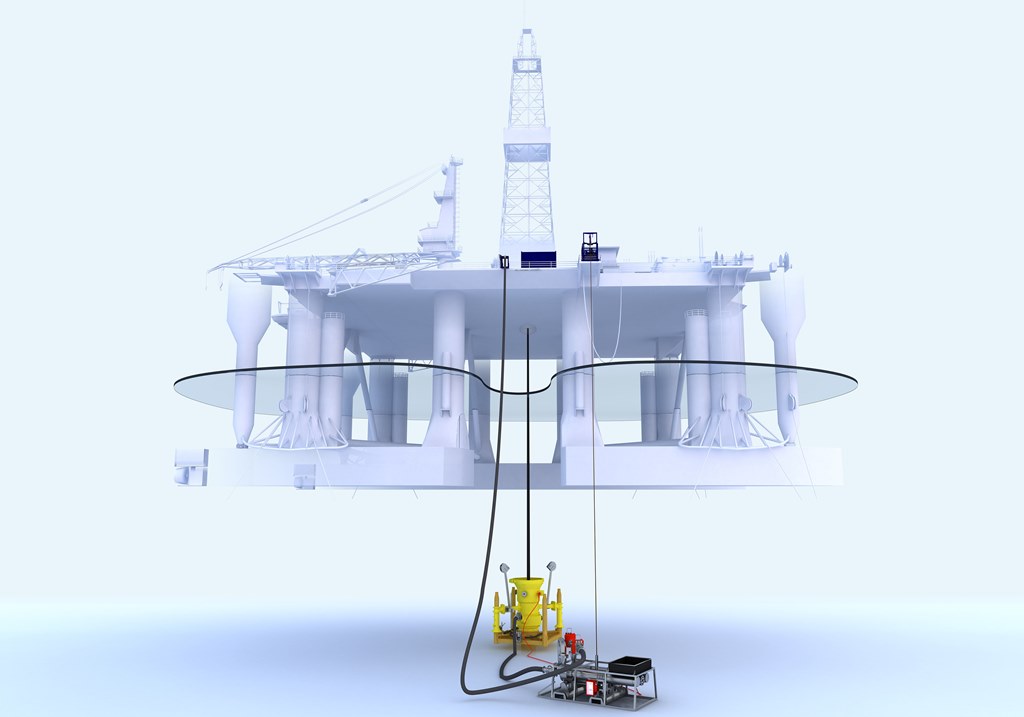

MPC®
The MPC® Managed Pressure Cementing system provides safe isolation of problematic zones - cost effectively - even in challenging narrow pressure window scenarios.